
Pre-fab home of the future, descended from the log cabin
The house of the future may be descended from Abe Lincoln’s cabin. Solid timber construction has practical and economic advantages, especially relating to accessory dwelling units (ADUs), a popular form of housing being legalized in states and cities across the US. Andres Duany of DPZ CoDesign became interested in log construction after becoming an expert in the challenges of building with prefabricated construction technologies.
DPZ won an Urban Guild Merit Award in Design Exploration for its C.I.E.R.S. (Compact, Independent, Economic, Residential System) Log House, a prototype of which was built on the National Mall this summer. Despite the widespread legalization, “surprisingly few ADUs have been built,” DPZ notes. “There are two possible explanations.
1. That those most in need of ADUs are not among the wealthiest and tend to have smaller backyards. This design is two stories which reduces the footprint of the ADU; thereby preserving a useful backyard area.
2. Most forms of prefabrication – including modular and SIP panels – require cranes from the street. In older neighborhoods, there is interference from overhead power lines and mature tree canopies. This is solved by log (solid timber) construction wherein each piece can be carried by two men via the sideyard.”
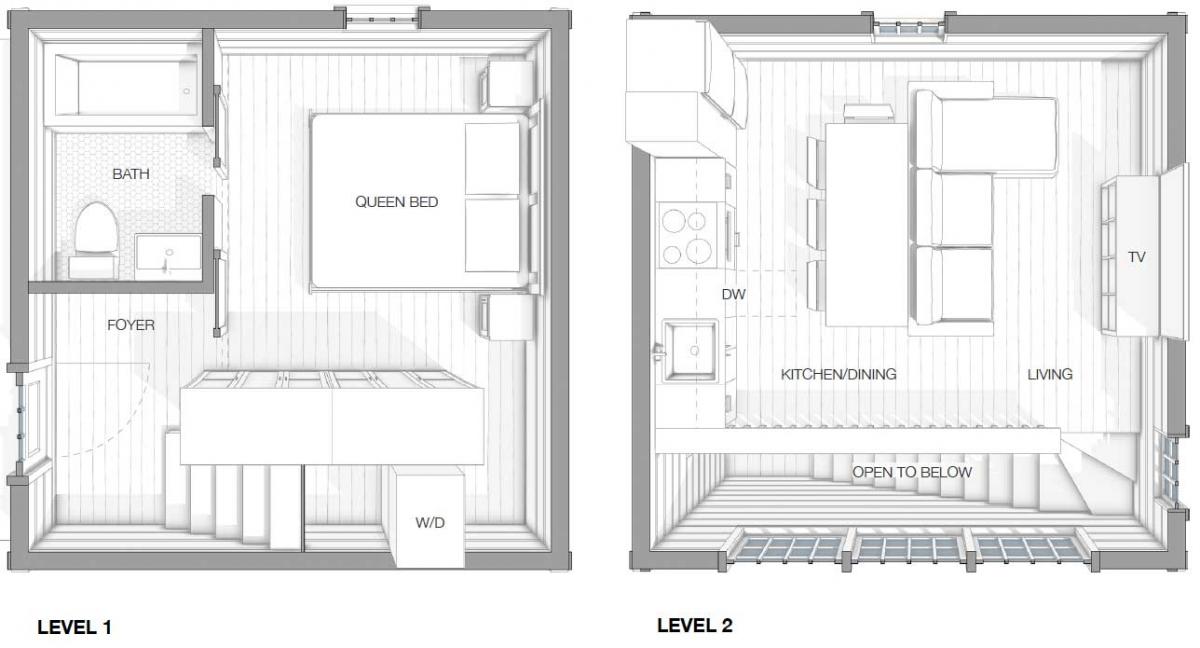
The log house was assembled, and the interior finished, with an untrained crew in approximately four days, DPZ explains. “We designed this 16-by-16-foot two-story ADU, had it fabricated in Canada, and delivered on site. The cabinets, kitchen appliances, bathroom, and furniture are from the local Ikea.”
The amazingly fast construction is explained by the one-step process of assembly, Dauny explains. The timber from the factory is numbered, notched, and the logs fit perfectly together in one step. They come with dry rubber seals and screws to tighten the seams if they ever develop gaps. “You can’t screw it up,” he explains. No drywall, insulation (they meet code), or paint is required. Contrast that with the 13 steps required for building conventional frame construction—and many of the steps involve wet applications of spackle and paint that require drying before the next step.
“Logs are an overlooked form of prefabrication technology – one which integrates structure, insulation, and finish (both interior and exterior). This contrasts with the separate layers and operations of the ‘sandwich,’ which is conventional 2x6 construction,” DPZ says.
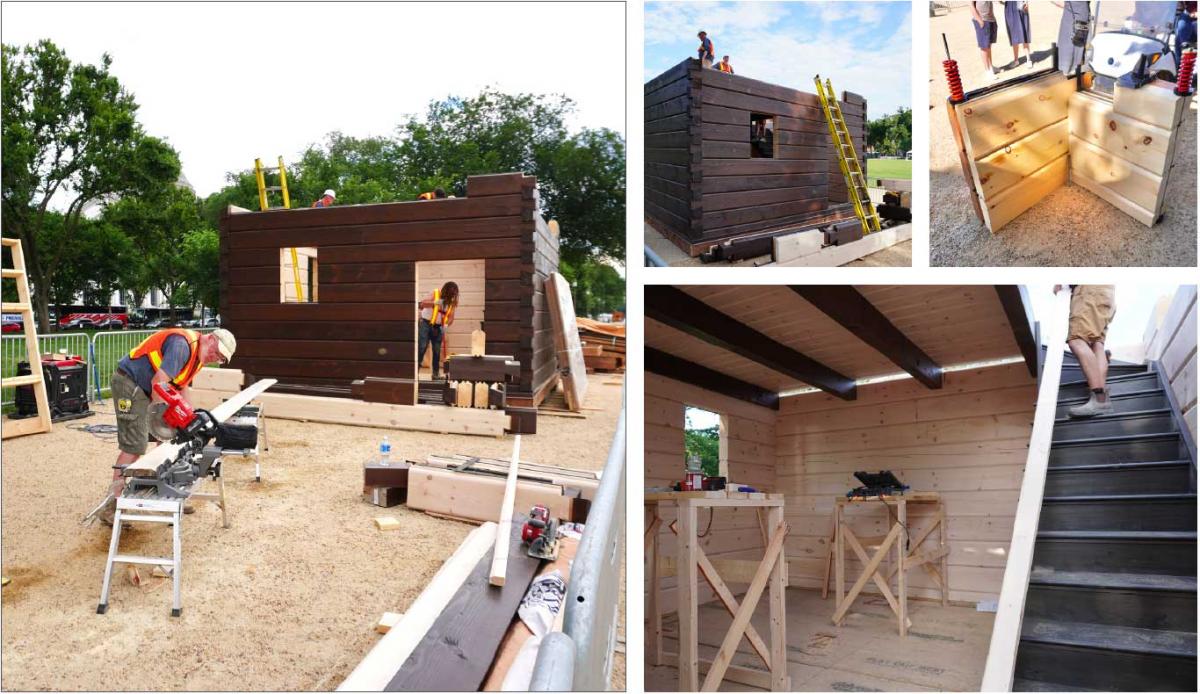
The log house also solves typical privacy concerns with regards to ADUs. Most of the windows are grouped on one side, where three large windows provide light for both floors. A handful of other small windows provide light and air without compromising privacy.
The main living area is on the second floor, with a compact kitchen/dining/living area. The first floor has a bathroom and bedroom. The roof is a low pitch, while the whole thing fits on a small slab.
Duany explains that his journey to the log house design began working in New Orleans after Hurricane Katrina, when DPZ was hired by Louisiana to explore new construction technologies including Structurally Insulated Panels (SIPs), styrofoam blocks, and others. None of them worked out because problems arose with the construction making them more complicated and expensive than they appeared. “Every single one failed. We had to build 450 houses stick built. I was so burnt by experience, I dropped out of using new technologies,” he says. Then he toured a solid timber construction material factory and had an “aha moment,” he says. That led to the prototype ADU on the National Mall, toured by thousands. The construction was funded by a Canadian developer, Max LeMarchant of New Amherst Homes, who suggested the two-story design.
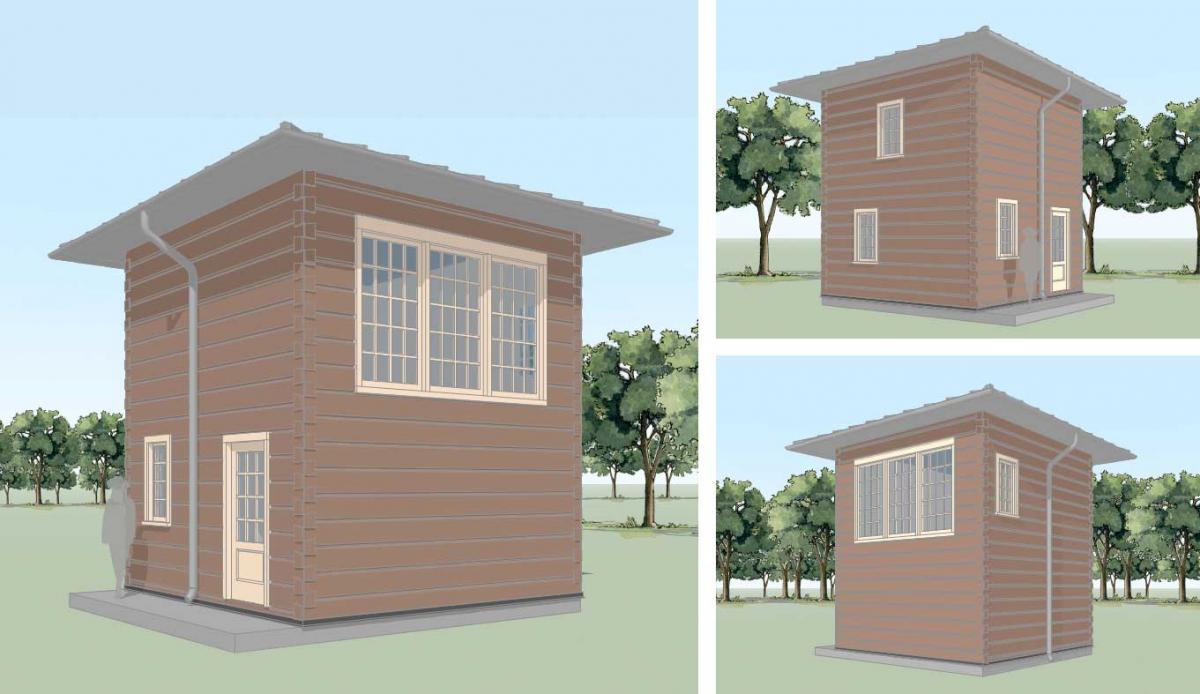
The C.I.E.R.S. Log House may be the most practical ADU design, if it can be brought to market at a reasonable price. “This ADU is thereby 100 percent prefabricated, so each piece of building and cabinet can be assembled by an untrained work crew,” according to the Guild. DPZ is now working with a developer or developers to make this design available for purchase. Moreover, it has a wider application than just ADUs. DPZ has also designed a single-family house using this material.
Disclosure: I was on the 2024 Urban Guild Awards jury, along with Sara Bega of Bega Design Studio, Rock Bell, East Beach Development, and Andrew Von Maur, a design consultant and professor at Andrews University.